Flexographic Plates
- Khobre Mihan co
- Article
- Flexographic Plates
Printing plates for modern flexographic presses are created using three distinct methods: rubber molding, photopolymer exposure and processing, and laser imaging. Although rubber molded plates have been in use since the 1930s, photopolymer plates, introduced in the 1970s, generally offer better resolution and more precise color alignment. Direct-to-plate laser imaging, known as ablation, can be used for both types of plates. The choice of plate type depends on factors like the type of press, plate cylinder inventory, and customer specifications, including resolution, registration accuracy, and cost considerations.
Molded Rubber
Rubber plates created through the molded rubber process undergo several steps, which include exposing and etching a magnesium plate, producing a mold, and subsequently transferring the image onto the rubber plate through the use of a molding press.
– Molded rubber plates experience shrinkage when they are taken out of the molding press. Plate films need to be adjusted to compensate for this shrinkage, which is typically around 1.5%-2.0% in the direction of the rubber grain and 0.5%-1% across it. It’s crucial to communicate the precise shrinkage percentages between production artists and plate makers.
– The line screening resolution is limited to 120 lines per inch (lpi).
– Achieving accurate registration can be more challenging compared to photopolymer plates.
– Nesting is necessary to create the illusion of a continuous repeat in the design.
– Creating precise rubber plates larger than 24″ x 36″ can be difficult. Larger designs must be arranged on multiple plates.
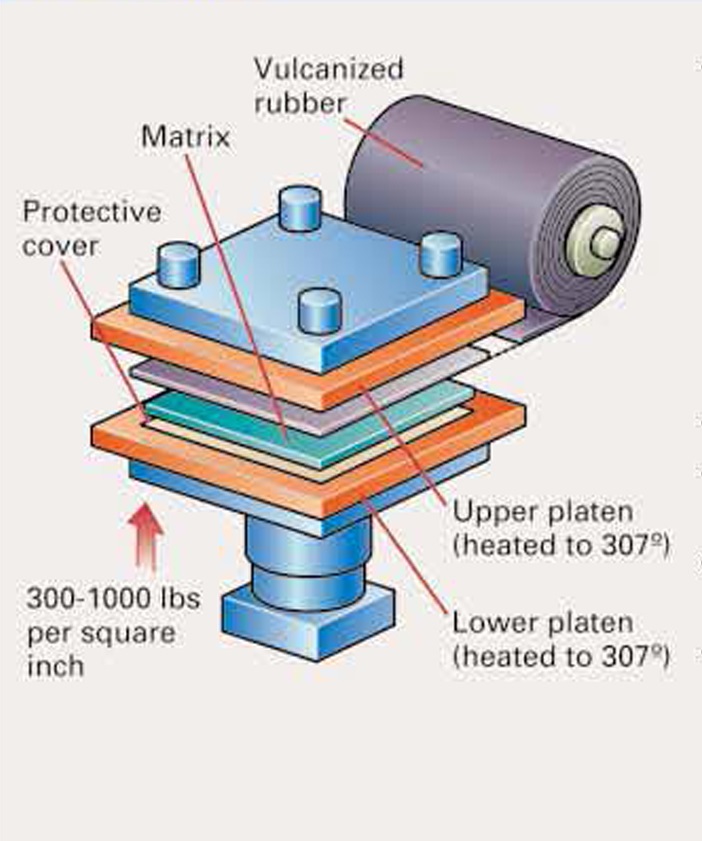
Photopolymer Plates
Photopolymer plates, which are light-sensitive, come in two forms: solid sheets and a thick liquid state. To create the image on the plate, the image area is exposed by using a film negative. The liquid photopolymer, which has a consistency similar to honey, hardens when exposed to ultraviolet light. Following exposure, the non-image area is eliminated through a processing step.
– Line screening typically ranges from a minimum of 150 lines per inch (lpi) to as high as 200 lpi.
– Nesting is essential to achieve the appearance of a continuous repeat.
– Most modern flexographic presses are equipped with positioning and registration devices primarily designed for one-piece photopolymer plates.
– Direct-to-plate laser imaging technology is accessible for plate production.

Laser Ablated Plates and Design Rolls
Certain platemaking machines have the capability to transfer images directly from a computer to the printing plate, which is referred to as “direct-to-plate.” This eliminates the need to produce film as an intermediate step. Additionally, some photopolymer plates can be directly imaged by lasers and subsequently processed using conventional methods. Another approach involves using a design roll, which is a cylindrical surface covered with either rubber or photopolymer material. These design rolls can be molded or imaged by a laser. They offer the advantage of creating a true continuous repeat with a seamless background color. However, when using laser-ablated plates, the plates must be nested to conceal the plate seam, ensuring the appearance of a continuous repeat pattern.
– Line screening is capped at 100 lines per inch (lpi) for reproducing tones, but it can be as high as 200-300 lpi for producing tints.
– The use of film is unnecessary.
– Design rolls can achieve a genuine continuous repeat with a continuous background color.
– Plates or design rolls imaged directly onto the cylinder do not necessitate adjustments for plate elongation.
– Laser ablating is a viable option for both rubber and photopolymer plate production.
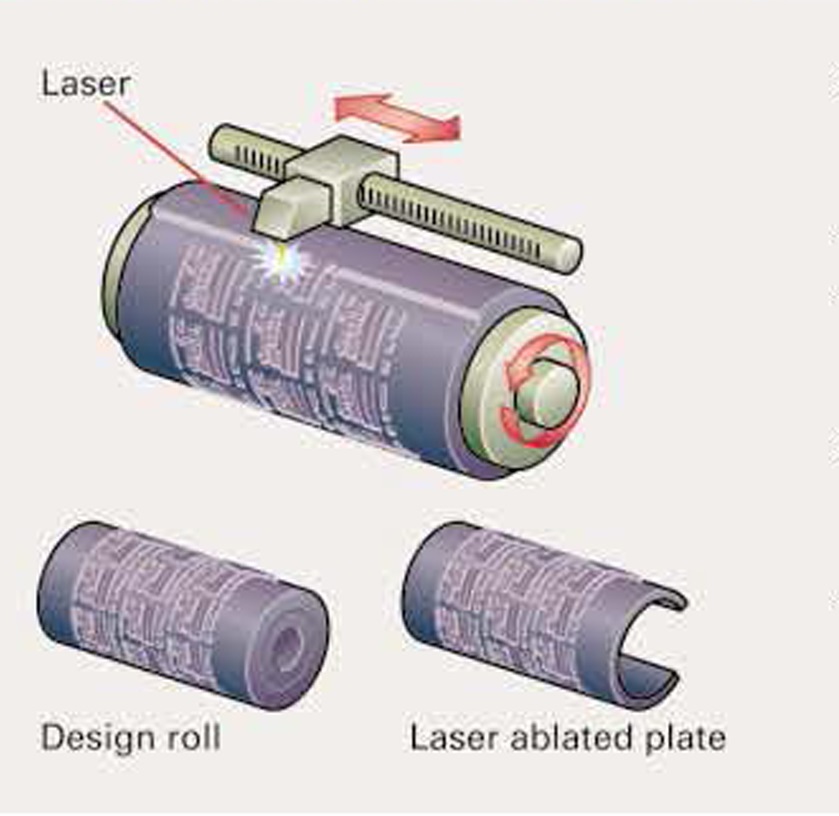
We help our customers stand out in the market by providing superior packaging solutions
To achieve this goal, we continuously invest in developing our relationships with our customers so that we can meet the needs of our customers today and tomorrow. The consulting and design team of Mehen’s expert engineers, after hearing the demands of the customers, examined the different ways of packaging the product and then using the valuable experiences of the past and the current knowledge of packaging and the use of new technologies, the most optimal type of packaging examined. provides to consumers. For more information and consultation with us, click on the free consultation button.