Step-Repeat and Die-cutting
- Khobre Mihan co
- Article
- Step-Repeat and Die-cutting
To optimize material costs and enhance productivity, the packaging industry employs a printing method known as step-and-repeat. This technique involves arranging various images, such as labels, on the printing plate to fully utilize its repeat length and cover the entire substrate width during printing. Often, nesting is necessary, where images are strategically staggered to maximize the repeat length and avoid plate seams. The plate ends are then cut to accommodate this arrangement. Nesting creates the illusion of a seamless repeat and is particularly useful for projects involving a continuous roll, like gift wrap.
Beyond maximizing substrate area, the strategic staggering of images also helps prevent a phenomenon called plate bounce. In flexography, where images are on the raised areas of the plate, bouncing can occur upon contact with an anilox roll or impression cylinder, potentially leading to skipped or misprinted areas or excessive inking.
Post-printing, most substrates undergo processes like cutting, folding, scoring, sealing, or gluing, often performed in-line. To ensure proper construction of the packaging, precise die-cutting specifications are essential for both the designer and the printer. For instance, a die-cut label or folding carton requires accurate positioning of all graphical elements. Packaging engineers frequently utilize Computer-Aided Design (CAD) systems for designing folding cartons, corrugated containers, or rigid paper boxes. Designers may also import the CAD layout to serve as a template for their designs.
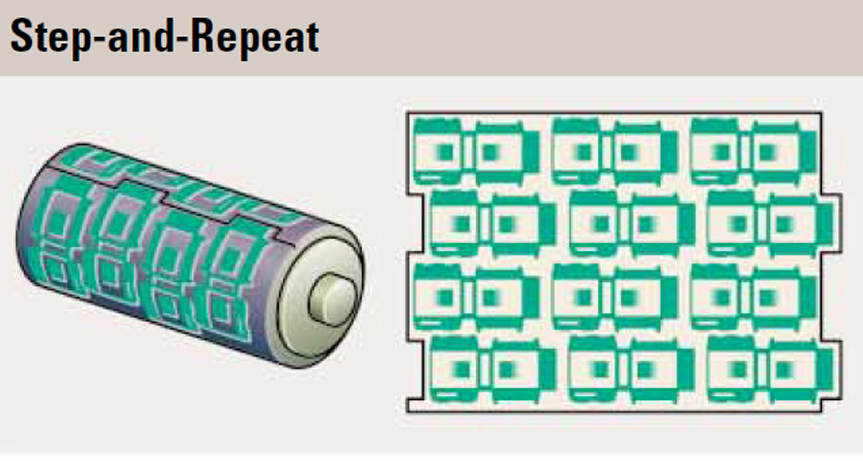
Arranging images in a nested fashion is an effective method to optimize the plate area and eliminate the plate seam in step-and-repeat printing. Design and imposition software provide step-and-repeat features tailored to specific repeat lengths and web widths.

Bleeds: To define bleeds, the designer needs to understand the locations where the packaging will undergo cutting, folding, and joining. Typically, bleeds extend beyond the fold and cut lines, but the exact amount of bleed is contingent on the printing press used.
Cut Areas: In instances where flexographic printers are linked to inline flatbed or rotary die-cutting processes, it is crucial to maintain registration between the die and the printed colors. To ensure precision, graphic elements should be positioned with a mindful distance from the designated cut areas.
Glue & Seal Areas: To guarantee proper sealing, areas designated for glue application should be devoid of ink and varnish, particularly those intended for heat sealing.
Score Lines: Die-cut folding cartons typically fold along score lines, and it’s essential for the designer to ensure precise registration at these points.
Varnish-Free Areas: Sections containing variable information, like freshness dates and product coding, must be void of varnish.
Windows: Die-cut windows for folding cartons or labels should be explicitly marked, but not all die-cutting machines may support them. Always verify with the printer before incorporating them into the design.
Bar Coding: To ensure accurate scanning by lasers, bar codes should be printed in alignment with the direction of the printing web and should account for dot gain.
Die-Cut Templates: Designers can export templates from CAD systems to illustration programs, which offers them a two-dimensional layout of the project.

Arranging images in a staggered manner on the plate can assist in maintaining continuous contact between cylinders, thereby reducing plate bounce. In certain cases, it may be essential to position non-printing bearer bars on non-image areas to preserve contact.
We help our customers stand out in the market by providing superior packaging solutions
To achieve this goal, we continuously invest in developing our relationships with our customers so that we can meet the needs of our customers today and tomorrow. The consulting and design team of Mehen’s expert engineers, after hearing the demands of the customers, examined the different ways of packaging the product and then using the valuable experiences of the past and the current knowledge of packaging and the use of new technologies, the most optimal type of packaging examined. provides to consumers. For more information and consultation with us, click on the free consultation button.