Flexographic Technology
- Khobre Mihan co
- Article
- Flexographic Technology
Flexographic printing units currently in use can be categorized into three fundamental types: the two-roll unit, the two-roll unit with a doctor blade, and the dual-doctor ink chamber system.
Two-roll units are typically found on older flexographic presses and narrow web presses. Narrow web presses equipped for process colors often incorporate the two-roll unit with a doctor blade, while more modern wide web presses utilize the dual-doctor ink chamber system. These different unit types cater to specific printing needs and technologies, with the choice depending on the type of press and the desired printing outcomes.
Every type of flexographic press incorporates an anilox roll. The surface of each anilox roll is meticulously engraved with a pattern of minuscule cells, so tiny that they are only visible under magnification. The size and quantity of these cells play a crucial role in determining the amount of ink delivered to the image areas of the plate and, consequently, to the substrate. Anilox rolls are typically fabricated using one of two methods: they are either copper engraved and then chrome-plated or made from ceramic-coated steel with a laser-engraved cell surface. These anilox rolls are vital components in controlling ink transfer and ensuring precise and consistent printing.
Anilox rolls are chosen with great care and consideration, taking into account the particular type of printing, the substrates being used, and the specific requirements of the customer. Flexographic printers frequently conduct test runs to identify the optimal anilox roll that can achieve the desired ink distribution for various printing elements such as halftones, spot colors, and solid areas. This meticulous selection process ensures that the printing results meet the exact specifications and quality standards set by the customer.
The design of the flexographic printing unit provides press manufacturers with the flexibility to construct presses in one of three primary configurations: the stack press, the inline press (which includes corrugated presses), and the common impression cylinder press. Each of these configurations can be equipped with any of the basic printing units, and the choice depends on the specific requirements and preferences of the flexographic printer. This adaptability allows for versatility in meeting a wide range of printing needs and applications.
Flexographic Ink Delivery System
In a two-roll flexographic printing setup, there is a rubber-covered fountain roll that rotates within an ink reservoir, drawing ink from the reservoir into the cells of the anilox roll. The pliable rubber fountain roll maintains close contact with the anilox roll. As the anilox roll revolves through a critical point, the fountain roll removes excess ink from areas without cells. After passing this point, each cell is filled with ink, ensuring a consistent and measurable ink supply for the printing plate. The metered anilox roll is brought into gentle contact with the plate’s image areas, while the plate cylinder makes contact with the substrate to transfer the image. The steel impression cylinder provides support for the substrate.
When a thin metal or polyethylene doctor blade is employed in this two-roll system, the point of contact between the fountain roll and the anilox roll is opened to allow ink to flood the anilox and fill the cells. The doctor blade then comes into contact with the anilox to remove excess ink from areas without cells. In cases where a dual doctor ink chamber is used, both the fountain roll and inking pan can be eliminated, and ink is directly supplied to the anilox through an enclosed chamber.

Characteristics of Anilox Rolls
Cell Per Inch (CPI) : The range for cell per inch (CPI) is from 140 to 1200. As the number of cells per inch increases, the amount of ink delivered to the printing plate decreases. When you have a higher line screen resolution, it’s advisable to also increase the CPI to maintain optimal print quality and accuracy.
Cell Volume : The range for cell volume is from 1.8 to 17 BCM (Billion Cubic Microns per square inch of cells). As the CPI (cells per inch) increases, the individual cell volume decreases.
Cell Angle : Standard anilox cell angles commonly used are 30°, 45°, and 60°. A 60° angle is preferred because it enables more effective ink transfer. However, it’s important to note that the combination of the screen angle of the printing plate and the cell angle can sometimes lead to the formation of a moiré pattern, even in single-color halftones. To prevent moiré patterns, separation screens are angled accordingly.
Application | Substrate | Cells Per Inch | Cell Volume |
Line art | Corrugated board | 200-280 | 7-8.5 BCM |
Halftones at 65 lpi | Corrugated board | 360-400 | 4.0-5.5 BCM |
4/c halftones at 133 lpi | Polyethylene bags | 600-900 | 1.8-2.0 BCM |
Press Configurations
Common Impression Cylinder (CIC) Press
- This press typically features 4 to 8 color units.
- It is primarily designed for one-sided printing.
- It excels at achieving precise and hairline registration, especially when operating at high speeds on stretchable films.
- Longer make-ready times are necessary due to the more challenging accessibility of the printing units.
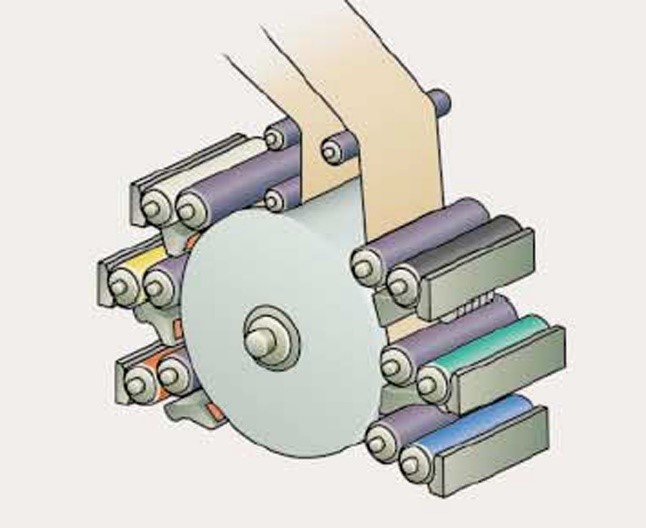
Stack Press
- These presses can have anywhere from 1 to 8 color units.
- Some of these presses have the capability to perform double-sided printing.
- To ensure quality results with thin films, traps (overlapping colors) should be no less than 1/64″.
- They are frequently used in inline setups with other converting operations, including lamination, rotary and flatbed die cutting, and side-seal bag converting.
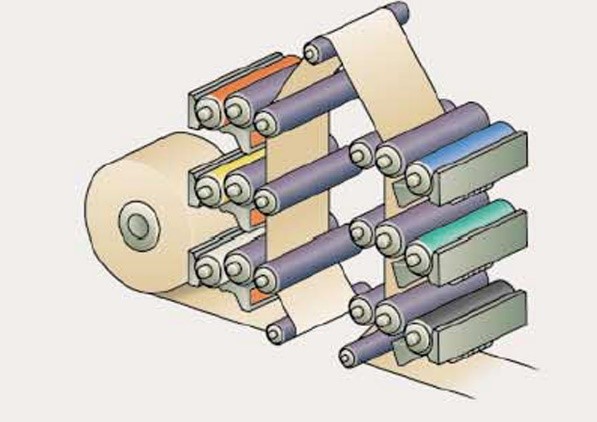
Inline Press
- These presses can feature as many as 12 color units.
- They have the capability to print on both sides with the assistance of a turn-bar.
- They are primarily employed for printing on thick materials such as paperboard.
- It is not advised for use in printing on thin packaging films.
- Frequently integrated into inl ine setups with other converting processes like lamination, rotary and flatbed die cutting, and side-seal bag conversion.
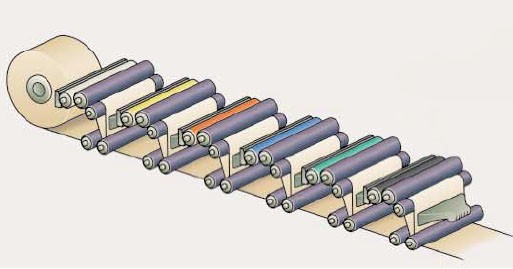
Corrugated Press
- This press shares the same configuration as an inline press.
- It is a sheet-fed press with the capacity to accommodate widths of up to 120 inches.
- Typically, it incorporates no more than 4 colors.
- It is primarily designed for one-sided printing.
- It offers less precise registration capabilities compared to some other presses.
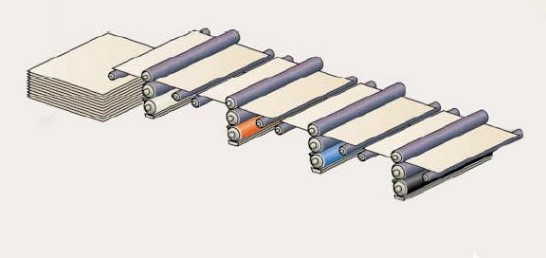
Repeat Length
Flexographic presses often feature plate cylinders with varying diameters, providing the flexibility to adjust the repeat lengths. When printing materials like gift wrap rolls for packaging, a continuous repeat pattern is used, where a set of images is replicated multiple times along an uninterrupted substrate. To prevent visible plate seams, it may be necessary to nest the images, arranging them in a staggered manner. This staggering of images creates a continuous appearance so that the design seems uninterrupted, regardless of where the substrate is cut.

We help our customers stand out in the market by providing superior packaging solutions
To achieve this goal, we continuously invest in developing our relationships with our customers so that we can meet the needs of our customers today and tomorrow. The consulting and design team of Mehen’s expert engineers, after hearing the demands of the customers, examined the different ways of packaging the product and then using the valuable experiences of the past and the current knowledge of packaging and the use of new technologies, the most optimal type of packaging examined. provides to consumers. For more information and consultation with us, click on the free consultation button.